Residual Stress Measurement
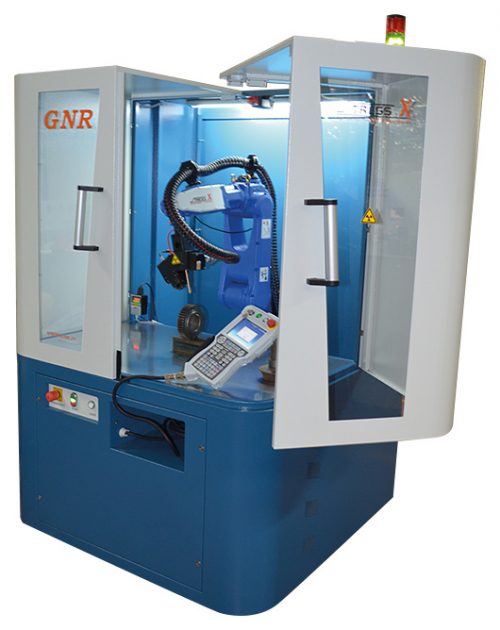
The StressX is a X-Ray Diffractometer designed specifically for Residual Stress Analysis. It provides a non-destructuve test of a sample. The head of the diffratometer is mounted on an anthropomorphic 6 axis robot that allows to analyse samples of any dimensions and shapes.
StressX could be mounted either in a closed cabin, suitable for laboratory analysis or on a four wheel trolley for on site analysis.
Residual Stress could be induced by machining, grinding, rolling, deep drawing, welding, thermal hardening and shot peening; its quantification allows to prevent fatigue damage and to control material’s durability and safety.
The StressX provides a flexible solution to residual stress determination on samples of any dimensions by the original synergy between compact X ray diffractometer and 6-axis robot.
6-axis robots are available with positioning accuracy and repeatability as low as 20 µm and positioning range as high as 895 mm radius from robot center.
Measuring target is defined by a combination of a Video camera for X-Y pointing and a laser for Z positioning.
Laser accuracy can be less than 10 µm and measuring range can be as high as 300 mm from the goniometer center.
Thanks to the 6 degree of freedom the measuring positions and angular ranges are only limited by robot size.
Some specific applications of the Stress-X are listed below:
- Detection of Residual Stress on sprocket wheels
- Detection of Residual Stress on car motor parts (cam axles, connecting rods, engine shafts, equalisers, …)
- Detection of Residual Stress induced by deep drawing (household appliances, structural parts, …)
- Detection of existing Operational Stress on gas conducts
- Detection of Operational Stress on large tensioned structures
- Measurement of efficiency of Shot-Peening and rolling of components subjected to Stress
- Definition of the quantity of Retained Austenite on bearings and parts of diesel motor injectors
- Detection of Residual Stress in castings (cast iron parts of tool machines and aluminium components)
- Detection of Stress induced by welding (laser and electron)
- Search for a correlation between residual stress and stress resistance of aluminium alloy car rims
- Optimisation of working parameters for swarf removal to improve the stress resistance of mechanical components
- Detection of Residual Stress on helicoidal and leaf springs
- Search for critical zones after applying work loads (arms and aeronautics)
Downloads
Our team of chemical analysts and technicians are on hand to help advise you on the machine which best suits your needs. For more information please fill out our contact form, email us or phone 0115 937 6686